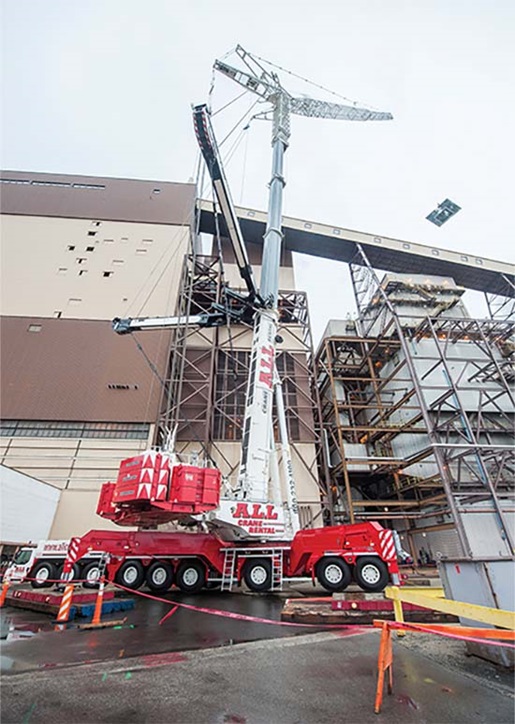
Construction work at plants and refineries can take the form of brand new construction, an expansion project, or a scheduled shutdown.
Each has its own challenges and requires the teamwork of trusted partners to achieve. Heavy lift equipment is often involved to set pipes, conveyors, and other processing and handling equipment. The ALL Family of Companies, the largest privately-owned crane rental and sales enterprise in North America, often gets the call.
Darrin Hogan, territory manager and sales representative with Dawes Rigging & Crane Rental, a member of the ALL Family of Companies, says preparing for plant work comes down to having the breadth of fleet to accommodate any situation; the right, qualified people on staff to execute the details; and experienced operators to conduct the lifts.
All terrain cranes and crawlers
All terrain (AT) cranes and crawlers are most commonly found in plants and refineries. Between those two crane categories, you typically find the correct mix of size, reach, capacity, and mobility required. Having a deep bench, like the ALL Family’s more than 3,600 pieces of lift equipment in its fleet, is vital to meeting the needs of plant work.
“For new construction, you’re often on virgin ground out in a field somewhere, and the multiple axles and grippy tires of ATs can handle dirt, mud, and even sand. This is also true of the tracks of a crawler,” said Hogan.
At higher capacities (400-, 550-, even 770-tons or more), ATs have the advantage of mobility and telescopic booms to work around obstructions. Lattice boom crawlers can handle heavier loads when space is less of an issue, and smaller-capacity hydraulic boom crawlers more easily fit into the nooks and crannies of plant sites for close-up work with smaller radii.
However, a new generation of AT has changed the game for squeezing larger cranes into tight quarters, expanding the ability to execute heavier lifts. “The VarioBase® capability of Liebherr ATs enables outriggers to be set at any position,” said Hogan. “This adds versatility for crane setup, getting us closer and tucking in tighter for the conditions we often encounter on the grounds of a plant or refinery.”
Another Liebherr feature is crab steering mode. It gives the driver the ability to seamlessly switch between standard steer and crab steer without needing to raise an axle. This feature takes job site mobility to a new level, where it can more easily maneuver between other equipment and structures. It is invaluable in power plants and processing plants, where tight areas are the norm.
Teamwork
Time is money, the saying goes, and this might be especially true during a plant shutdown. A predetermined amount of work must happen within a limited amount of time. Too little work completed or too much time taken immediately starts racking up unwanted costs for the plant owner.
It’s the people behind the machines who make the real difference in pulling off a series of successful lifts. “Here at Dawes, we have engineers on staff who can deliver stamped lift plans,” said Hogan. “That is an incredible luxury for our customers – but it becomes almost a necessity given the narrow timelines for many plant outages.”
Hogan recalls a certain project in which state and local engineers had a week’s long backlog of plans to certify, but the material to be lifted was arriving in mere days. Because the Dawes engineers had already been working on the lift plans for weeks, they were able to stamp the plans with hours to spare before material arrived. “Otherwise, there the material would sit, awaiting cranes, while the customer accrued unplanned costs.”
Then there are the people actually behind the controls of the cranes, ALL’s own operators. Hogan recalls a recent series of dual picks requiring operators to work within tight tolerances while using cranes with capacities of 550 tons or more. “They were picking pieces of plant equipment that weighed 201,000 and were 110 feet long. They had to maneuver them inside a partially completed building. At the point of entry, they couldn’t have had any more than six inches of clearance on either side. It’s a real art.”
This type of work requires a steady hand, laser focus, and years of experience. In the midst of an already complicated lift, both operators also had to swing their cranes 180 degrees in unison before setting the giant pieces.
Preparation
Members of the ALL team are onsite weeks and often months before lift days, conducting site visits, taking precise measurements, gauging ground bearing pressures, and becoming familiar with any obstructions or special circumstances surrounding the lift area.
For long-term rentals, which can exceed three, six, and even 12 months, ALL can embed not only a full-time safety team onsite, but also a dedicated maintenance team to maximize machine uptime.
“Careful preparation saves time in the long run,” said Hogan. “It results in accurate 3-D lift plans, makes daily lift meetings go smoother once the project has begun, and helps everyone focus on what will be done on the day of the lift.”